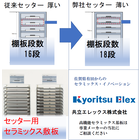
焼成プロセスに、最適化した「セッター用セラミックス基板」で フェライト基板や金属粉末射出成型(MIM)製品の焼成お手伝いします
焼成プロセスで用いられる「バッチ式真空焼成炉」での生産効率の改善は大きな課題です。 1つの目のご提案は、「多段積み」による焼成プロセスの生産効率改善です。 従来のセラミックス敷板(7mm厚)を「当社の焼成セッター用セラミックス基板(1mm厚)」に変えることで、棚板段数を16段から18段に増やすことが可能となり、12%も焼成積載効率が改善されます。 また、同じワーク数でも「より厚いワーク」が焼成可能となり、焼成炉の幅広い活用が可能となります。 2つ目のご提案は、「微小凸型の多孔質セラミックス加工」です。 焼成品質に影響を与えるプロセス条件の中で「脱媒性能・特性」は重要で、種々の多孔質セラミックス材料の活用が工夫されています。 これら多孔質セラミックス基板技術に加えて、「微小凸型の多孔質セラミックス加工」を施したセッター用セラミックス敷板を用いることで、焼成ワークの底面部にスペースが確保できることから脱媒効率や脱媒性能が改善されます。
焼成プロセスで用いられる「バッチ式真空焼成炉」での生産効率の改善は大きな課題です。 1つの目のご提案は、「多段積み」による焼成プロセスの生産効率改善です。 従来のセラミックス敷板(7mm厚)を「当社の焼成セッター用セラミックス基板(1mm厚)」に変えることで、棚板段数を16段から18段に増やすことが可能となり、12%も焼成積載効率が改善されます。 また、同じワーク数でも「より厚いワーク」が焼成可能となり、焼成炉の幅広い活用が可能となります。 2つ目のご提案は、「微小凸型の多孔質セラミックス加工」です。 焼成品質に影響を与えるプロセス条件の中で「脱媒性能・特性」は重要で、種々の多孔質セラミックス材料の活用が工夫されています。 これら多孔質セラミックス基板技術に加えて、「微小凸型の多孔質セラミックス加工」を施したセッター用セラミックス敷板を用いることで、焼成ワークの底面部にスペースが確保できることから脱媒効率や脱媒性能が改善されます。