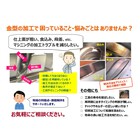
現場の問題点や課題解決をサポート!! 金型の加工で困っていること、悩みごとはございませんか?
□ マシニングの加工トラブルを減らしたい。 □ 品質的な不具合を減らしたい。寸法が出ないのは機械の問題? □ 食込み・段差など 対策してもなくならない。 □ 現状の加工方法は合っているのか? □ 間違った判断でプログラムを作成していないか? □ 工具や条件は適正なのか? 工具の寿命を延ばしたい。 □ 再研磨に出すタイミングの判断が難しい。 □ チャックやホルダーの正しい使い方は? □ 切削加工の知識を深めたい。 □ 効率の良い加工方法を知りたい。 □ 新人や若手社員のベテランとの技量の差を無くしたい。 □ プログラム作成時間を短くしたい。間に合わないことがある。 等々 当てはまる項目がありましたら、お気軽にご相談ください。
□ マシニングの加工トラブルを減らしたい。 □ 品質的な不具合を減らしたい。寸法が出ないのは機械の問題? □ 食込み・段差など 対策してもなくならない。 □ 現状の加工方法は合っているのか? □ 間違った判断でプログラムを作成していないか? □ 工具や条件は適正なのか? 工具の寿命を延ばしたい。 □ 再研磨に出すタイミングの判断が難しい。 □ チャックやホルダーの正しい使い方は? □ 切削加工の知識を深めたい。 □ 効率の良い加工方法を知りたい。 □ 新人や若手社員のベテランとの技量の差を無くしたい。 □ プログラム作成時間を短くしたい。間に合わないことがある。 等々 当てはまる項目がありましたら、お気軽にご相談ください。